The Fundamentals of 2-piece Disc Attachment Methods
06.10.2024Fundamentals of 2-piece Disc Attachment Methods
As is the case with most metal, iron brake discs grow substantially when heated. Expansion can increase the thickness, diameter and circumference, and one-piece disc designs run into problems when this occurs. Look at the picture below and imagine the disc is being heated on the track. As the disc expands, the outer edges of the disc are pulling away from the center of the disc, but there are no built-in provisions to allow for that expansion. The edges of the disc therefore pull, lift, and distort, which is called coning. Now imagine that disc vertical on the car, running in your caliper. Coning directly impacts the brake pads’ contact with the disc, leading to uneven wear and tapering, and even a long brake pedal.
Two-piece discs on the other hand, compensate for the expansion of the disc as it heats. This is accomplished by building ‘float’ into the 2-piece disc assembly, allowing the disc to run true inside the caliper and reducing distortion, stress cracks, and pad taper.
Traditionally, this float is built into either the disc itself or the disc hat/bell. This is commonly referred to as a disc’s ‘attachment method’, ‘mounting system’, or ‘drive system’. On a float-in-disc assembly, the iron disc ring has an oblong hole or channel in which a stainless steel bobbin slides as the disc heats and expands (Figure A below). In a float-in-hat assembly, the disc bobbin slides in a channel cut into the aluminum hat (Figure B below). With both disc drive methods, the iron disc ring typically has 10-12 mounting tabs cast into its outer face to which the aluminum hat is bolted (Figure C below). On an assembled disc being run in competition, those mounting tabs are responsible for completely bearing the load being placed on the disc.
Figure A: Float-in-disc attachment method (used in Essex Competition Brake Kits)
Figure B: Float-in-hat attachment method (used in Essex Road Brake Kits)
Figure C: Traditional bobbin drive mounting tabs
Mounting Hardware and Anti-Knockback Spring Clips
If you look closely at the mounting hardware we use in our Competition Kits, you’ll notice a few details that are often overlooked in lesser products. These components are specially made for their intended purpose. These are not cheap bolts found at your local big box store. They are custom made in the USA for Essex and AP Racing, and they are the exact same components we use on professional racing products.
As discussed above with regards to the piston springs, knockback can be a serious issue when tracking a car. In order to help control the lateral motion of the disc, which pushes the pistons back into the caliper, we use an anti-knockback spring clip on every other disc attachment point (on a ten bolt disc there are five spring clips, while on a twelve bolt disc there are six). These spring clips help keep the disc hat and iron ring in alignment, while still allowing the disc to expand and float radially. As an added bonus, they prevent the hat and iron disc from rattling and making noise.
Hat Design
Floating two-piece discs also have the added benefit of reducing heat conduction to the hubs and bearings, decreasing wear and tear on these costly components. The disc hats themselves are manufactured from 6061 heat-treated billet aluminum, with a hard anodized coating. This material was specifically chosen for its strength at high temperatures, as it will be in direct contact with the searing hot iron discs. The hats feature scallops on the underside, to allow for heat evacuation along the outer disc face once installed.
Spline Drive Attachment Method (used in Porsche GT3 Cup and GT4 Clubsport 2-piece Discs)
The Essex Spline Drive mounting system uses technology from current pro racing discs and has several advantages over traditional attachment methods. Rather than 10 to 12 mounting tabs with slots machined out internally for bobbins, there are 20 smaller mounting tabs that function as slots themselves. Instead of a steel bobbin providing float at each mounting point, it is accomplished with iron tabs that mesh seamlessly around the disc with the corresponding aluminum tabs of the hat. In this manner, the entire disc assembly is both simplified and strengthened.
Our Spline Drive system eliminates the need for any type of bobbin, while also dispersing stresses across twice as many locations on the disc. The interlocking tabs not only provide the necessary room for radial float as the disc heats and expands, but also act as splines to directly transfer the torque under braking.
With the tabs handling load transfer, the fastener portion of the new Spline Drive assembly is quite different and much simpler. On a traditional float-in-disc design (below), each of the 10 to 12 load-bearing fasteners is pulling double duty, and must be thick enough to transfer brake torque and hold everything together at the same time.
The Spline Drive system eliminates half of the pieces found in a traditional bobbin drive hardware stack. Whereas our float-in-disc stack contains six pieces (below left), our Spline Drive setup requires only three: a bolt, retainer, and jet nut (below right). Since they are not load-bearing, the new fasteners are smaller in thickness at 5mm and don’t require as high of a torque value. Finally, when swapping to fresh replacement iron rings, only the jet nut must be replaced each time, reducing the cost of consumables.
New Spline Drive Hardware Design:
To provide axial float that also mitigates knockback and offers consistent pedal effort, we've integrated float-control springs into several recesses in the aluminum hat. They are completely encapsulated once assembled, so there's less of a chance for these springs to be bent or damaged vs. traditional anti-knockback (AKB) spring clips.
Another unique benefit of the Spline Drive system is an extremely low profile on the inside of the disc assembly, providing an undisturbed entry path for cooling air through the vanes (see below).
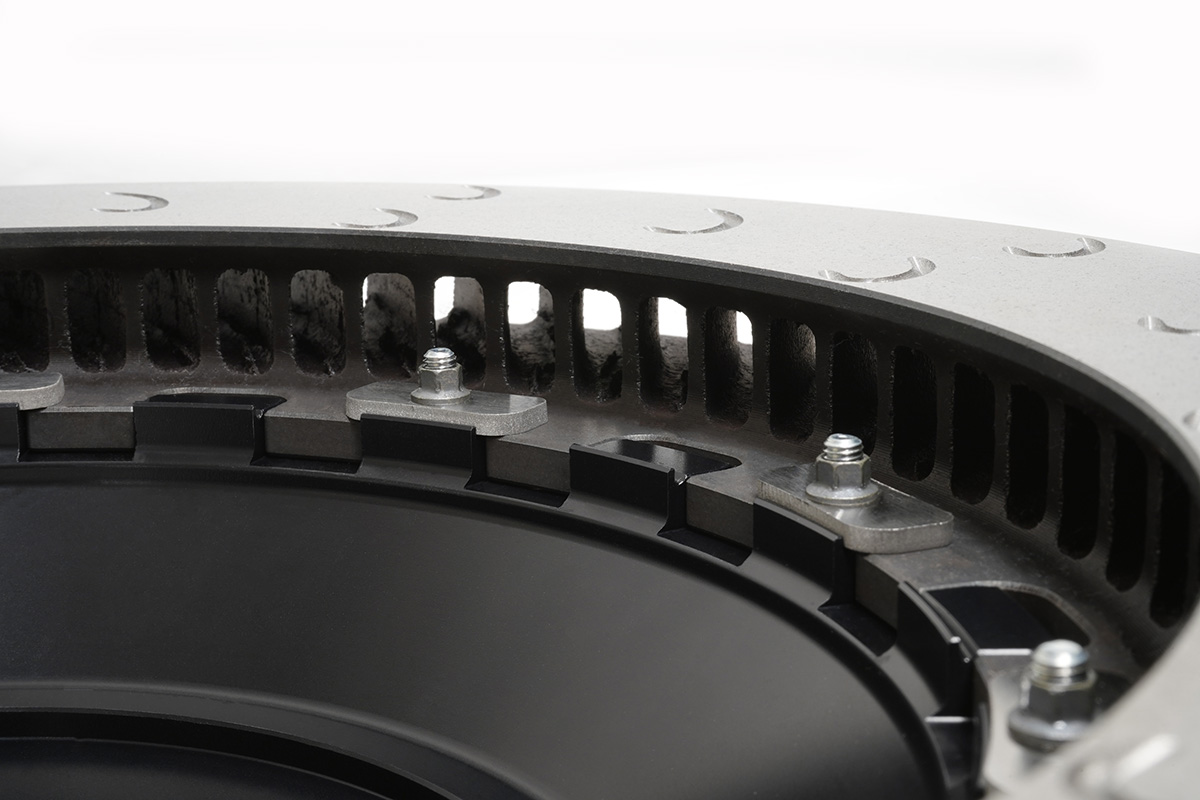
Finally, the elegant hardware packaging provides an incredibly clean aesthetic when viewed from the outside. The only visible piece of hardware is the bolt head, and everything else is hidden inside the disc.
Customer Comments:
No comments posted yet
You must be logged in to leave a Comment